Today, structural repairs of composite parts are still done in the traditional way by bolting a metal panel over the damaged area, but the effects of the repair on the quality of the material in the long term is unclear. The ‘Bonded Repair’ can offer a better method by gluing a composite patch in or over the damaged area. This has the potential to restore both the rigidity and the strength of the material for 100% and retain the smooth outer contour, so that the composite remains aerodynamic.
Innovation Track 1: Developing a certified composite repair method
The aim of this innovation track is to develop a certified method for so-called ‘Bonded Repair’ of composites. By conducting research into methods for certification of the adhesive bonded repair, including the use of Structural Health Monitoring (SHM) systems, a representative demonstrator will be designed, manufactured and tested. The project focuses on the bolt free repair of aerospace primary structures using composite patches adhesively bonded to the damaged area. The objective is to investigate and define materials and repair processes capable of restoring the operational capability of the damaged structure in compliance with the airworthiness certification requirements.
Advantage DCMC
A big advantage of performing this innovation track within the framework of the DCMC is that the parties involves in the DCMC together have all of the knowledge regarding certification, material properties and gluing methods to successfully perform this project.
Certified bonded repair
After conducting research into methods for certification of the adhesive bonded repair, a representative demonstrator was designed, manufactured and tested. In November 2018, the repair was made on a demonstration panel representing the NH90 stabilizer. As a next step, static and dynamic tests were performed. This project has proven that the method works and can be used to certify a bonded repair using the Equal Level of Safety (ELOS) procedure. The demonstrator panel was successfully tested in April 2019.
Next step
The major drawback of this approach, however, is that a complete loss of the repair patch is not prevented and that according to the present airworthiness requirements the repair size is limited to damaged structures that still can take Limit Load (LL) after complete loss of the patch. Therefore, follow up research will be performed into certification methods to be used for larger sized damages in composite structures.
Panel
Panel test
Mode I test
Mode II test
Project status
Runtime: March 2017 – 2019
Project closed
- May 2017
- Nov 2017
- Apr 2018
- May 2018
- Aug 2018
- Nov 2018
- Apr 2019
Milestone 1: Literature review
As there are many composite materials and repair methods in use a selection of a representative demonstration platform is needed. The repair of a sandwich structure was selected to demonstrate the repair and airworthiness certification of the repair.
Milestone 2: Determining the demonstration structure
As there are many composite materials and repair methods in use a selection of a representative demonstration platform is needed. The repair of a sandwich structure was selected to demonstrate the repair and airworthiness certification of the repair.
Milestone 3: Determining the materials and material properties
The material properties are needed to analyse and design the repair. The properties were partly obtained by literature review and partly by performing mechanical tests.
Milestone 4: Determining the certification approach
As there are no standard certification methods available for adhesive bonded repairs on aerospace structures alternative certification methods have to be investigated. Finally an approach was found were the initial bond strength was substantiated by testing of traveler patches surrounding the repair patch together with an in-service monitoring of the repair patch behaviour by a dedicated SHM system.
Milestone 5: Design and analysis of the repair
Methods have been developed for a quick assessment of the remaining strength of a damaged structure and the restored strength in case of a bonded patch repair. Within this milestone the demonstrator repair was designed and analyzed.
Milestone 6: Manufacturing of the demonstration repair
The repair was manufactured and the repair demonstrator is ready for testing.
Milestone 7: Demonstrator test (in progress)
Execution of the static and fatigue test program.
Partners involved
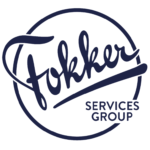
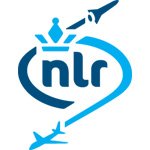
More information
For any questions about the project (status) or if interested to collaborate, please contact:
Henk Jan ten Hoeve (NLR) Henk.Jan.ten.Hoeve@nlr.nl or Marcel Bos (NLR) marcel.bos@nlr.nl