Nowadays, the manufacturing of aerospace composite structures is done in a high-tech production environment using robotic equipment for processing and assembling aerospace (sub) structures. The certification according to stringent airworthiness requirements is done based on these automated and controlled manufacturing processes. But in case of damages to these composite structures, repair can only be done by manual repair processes. These are less reproducible compared to the automated and controlled manufacturing processes.
The challenge is to develop automated repair methods and processes with a reproducibility similar to the manufacturing processes. To reach this target, a lot of fundamental and industrial research work needs to be done. Shortening the repair time is necessary because the amount of time an aircraft can stay on the ground for repair is limited. Automation is necessary to shorten the repair time and allow for customised replacement of the material by working with very accurate lasers.
Innovation Track 6: Automating the repair process
The aim of this project is the automation of the abrasion process. As a result, in the repair process, the automated removal of the damaged composite material including coating will be many times faster than by manual removal.
Three methods will be selected and evaluated in the project:
- Milling
- Water jet abrasion
- Laser ablation
Innovation track 6 has been split between NLR and Fokker Services. NLR focusses on milling and water jet abrasion, while Fokker Services focusses on laser abrasion. All three methods are used to remove composite material and to create a scarfed pocket around the damaged area. The repair will take place by adhesive bonding of a cured or prepreg patch into the pocket.
Milling & water jet abrasion
NLR has investigated the automation of the milling process by evaluating the available milling robot (MobileBlock from DMGMORI) and water jet equipment (from AWJ). Both methods have proven that the technology works to mill cut-outs (scarfed and stepped). However, there are practical implications to use the equipment on curved surfaces or on smaller structures due to the size of the tooling and/or processing time.
Currently, NLR is working on an alternative method for an automated inspection/repair procedure using thermographic inspection and sanding/milling of the damaged area. This method makes use of the Universal Robot UR16e collaborative robot (cobot) system with a sanding head and an NDI system consisting of a FLIR Infrared camera and IR lightning. A 3D geometry measuring scan system is also planned to be coupled to the cobot. The NDI data will be merged with the 3D scan data by using the technology developed in innovation track 5. This data will be used to generate the control file for the sanding head.
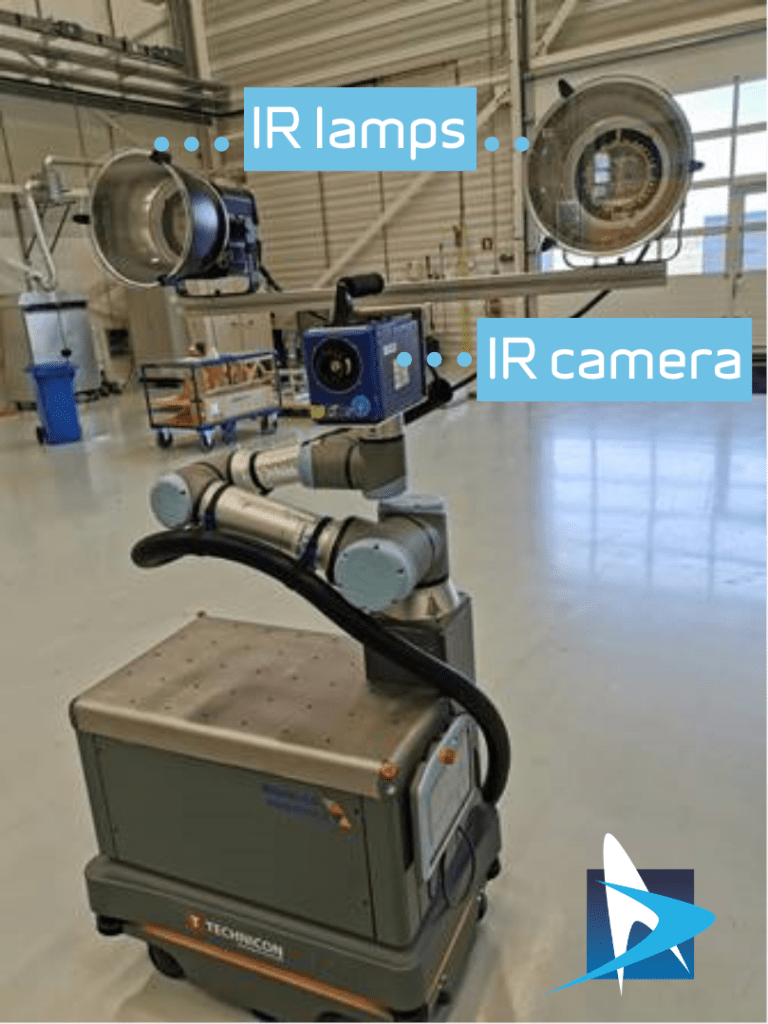
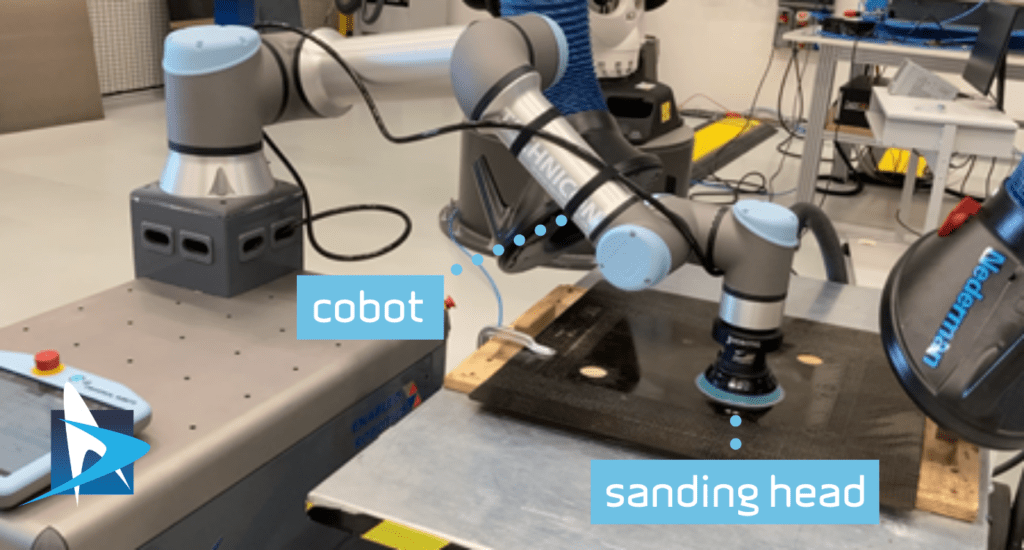
Laser ablation
The third technique, led by Fokker Services, is the use of laser ablation, using a high power laser to remove surface coating such as paint and primer as well as damaged matrix/fibres of a composite structure. The laser ablation technology is developed and thoroughly investigated, showing that it is possible to create a very accurate cut-out with a clean surface that can be used for adhesive bonding without further surface treatment.
For this purpose, the available laser equipment at Fokker Services will be developed further to demonstrate the automated laser ablation technique on double curved surfaces as well. Since almost all aircraft parts are double curved, this is essential for applications on an aircraft or other equipment built from composite material. Besides, for full depth repair, the preparation for shallow repairs used for (stone) impact damages will also be investigated.
In order to make this technique accessible to the industry in a practical way, the research project will also include the development of tooling that can be used in an industrial (MRO) environment.
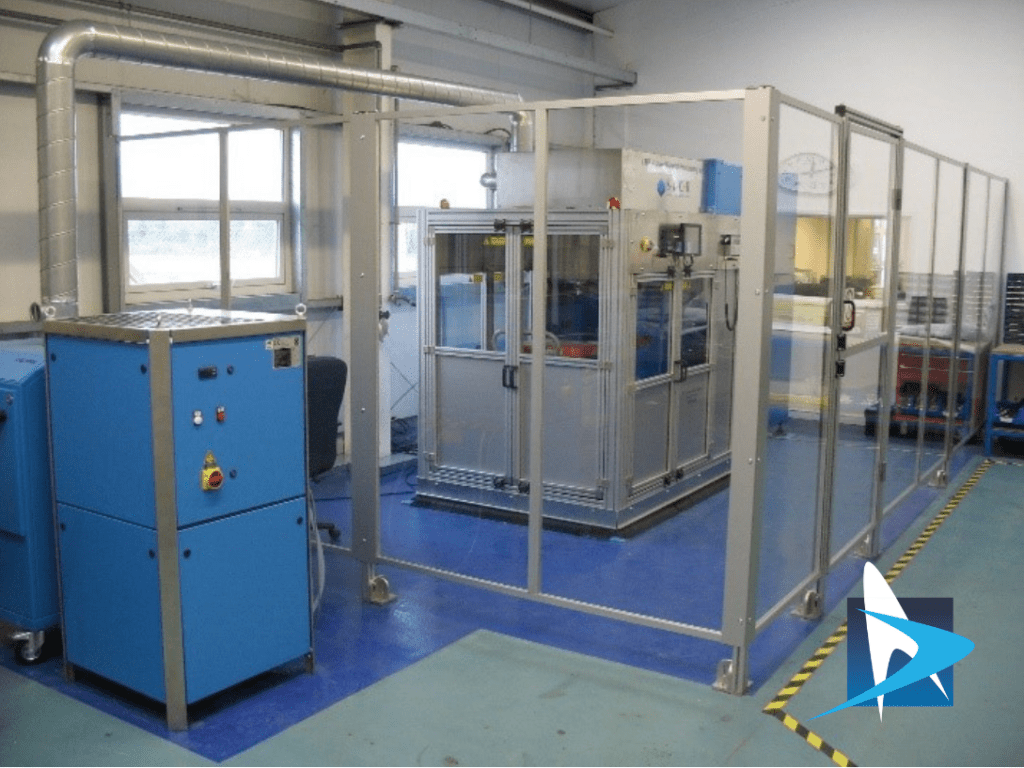
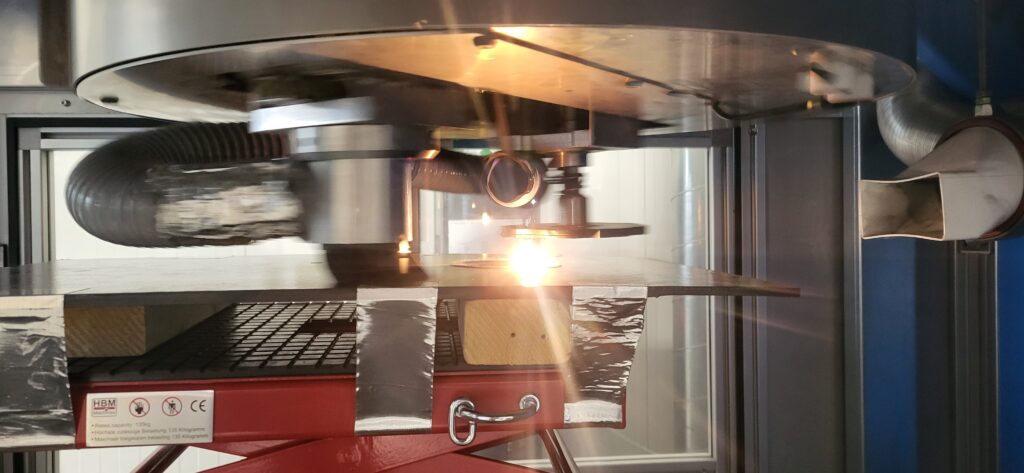
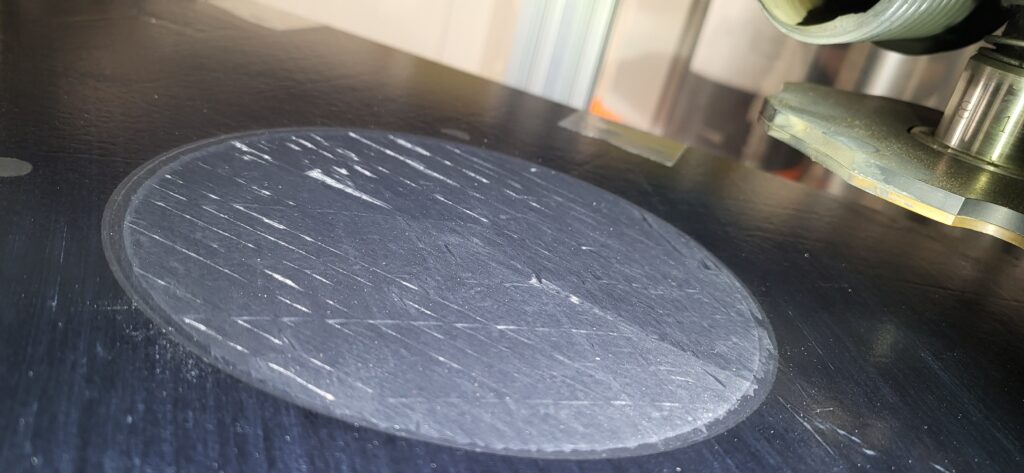
Project status
Parties involved
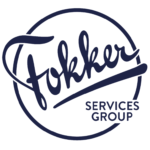
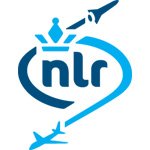
More information
For any questions about the project (status) or if interested to collaborate, please contact:
- Henk Jan ten Hoeve (NLR) Henk.Jan.ten.Hoeve@nlr.nl or Hotze Jongstra (NLR) hotze.jonstra@nlr.nl.
- Mark Kerkhoven (Fokker Services) mark.kerkhoven@fokkerservices.com.